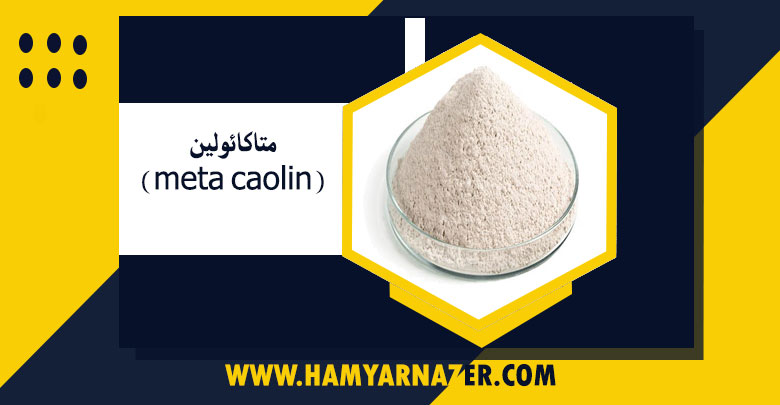
متاکائولین(meta caolin)
بتن، رایج ترین ماده کاربردی در صنعت ساختمان در جهان است که مخلوطی از دو جزء اصلی شامل مصالح ریزدانه و خمیر چسباننده می باشد. در سال های اخیر، تحقیقات و اصلاحات زیادی به منظور تولید بتن با خصوصیات و ویژگی های مطلوب انجام شده است و نیز برای رسیدن به بتن یا کارآیی و مقاومت بیشتر ادامه دارد. متاکائولین یکی از فرآورده های رسی است که پس از ابداع، در سال های اخیر رشد یافته است. متاکائولین، به واسطه تکلیس کائولین خالص (رس معدنی) طی عملیات حرارتی کنترل شده ای در درجه حرارت ۸۰۰-۶۵۰ درجه سانتیگراد بدست می آید. متاکائولین یک پوزولان بسیار فعال با سطح ویژه زیاد است و به همین دلیل می تواند به عنوان جزئی از مواد تشکیل دهنده سیمان بعنوان یک ماده چسباننده، جایگزین بخشی از حجم سیمان گردد. از آنجا که نگرانی های زیادی در خصوص مقاومت و پایایی بتن، وقتی که متاکائولین به عنوان ماده ساختمانی در صنعت ساخت و ساز بکار گرفته شود، وجود دارد لذا باید انجام مطالعات در راستای تعیین سهم متاکائولین در میزان عملکرد و سطح کارآیی و دوام بتن صورت پذیرد. اثبات پایایی و توانمندی بتن حاصل، به جایگزینی متاکائولین به جای بخشی از سیمان منجر خواهد شد.
وقتی متاکائولین در بتن استفاده می شود طی واکنش پوزولانی با آهک هیدراته، تبدیل به سیلیکات کلسیم هیدراته می گردد. استفاده از متاکائولین به عنوان ماده جایگزین بخشی از سیمان در ملات و بتن در سالهای اخیر بطور گسترده ای مورد مطالعه قرار گرفته و اخیراً این موضوع، کلیه کانی های سیلیسی- آلومینی را که دارای ذرات بسیار ریزی هستند در بر می گیرد که در حضور آب با هیدروکسید کلسیم واکنش داده و حاصل، ترکیبی با خواص سیمانی می باشد اما با این وجود، هنوز ناشناخته های زیادی در خصوص استفاده از متاکائولین وجود دارد.
با توجه به خواص پوزولانی متاکائولین، می توان آنرا جایگزین بخشی از سیمان مصرفی و جزئی اصلی در بتن نمود. ذرات متاکائولین تقریباً ۱۰ برابر کوچکتر از ذرات سیمان هستند که کاربرد آنها در بتن، منجر به چگالتر شدن بتن و غیر قابل نفوذتر شدن بتن در برابر آب می شود. استفاده از متاکائولین، مقاومت و پایایی بتن را در برابر حمله های شیمیایی، سولفاتها و انبساطASR و چرخه های یخ زدن و آب شدن افزایش می دهد. متاکائولین همچنین در بهبود برخی از خواص مکانیکی بتن شامل مقاومت فشاری، خواص کوتاه مدت و مقاومت خمشی موثر است.
بر عکس سایر پوزولان ها، متاکائولین محصول فرعی نیست و ارزش های مهندسی آن بخوبی کنترل شده است. بنابراین استفاده از متاکائولین در مقایسه با سایر مواد جایگزین سیمان، مزایایی دارد که نیازمند مطالعه روی بتن متاکائولینی می باشد.
کائولین
نام «کائولین» از واژه چینی Kauling به معنی تپه بلند، گرفته شده که نام تپه ای در نزدیکی Jauchan Fu است و قرنها پیش، این ماده برای سرامیک سازی از این محل استخراج شده است.
اجزای اصلی تشکیل دهنده کائولینیت، سیلیکات آلمینیوم آبدار با ترکیب تقریبی ۲H2O.Al2O3.2SiO2 می باشد. کائولینیت، کانی رسی است که از مواد خام شکل پذیر بدست می آید و سپس طی گرمایش تبدیل به یک ماده پایدار می گردد. از لحاظ ساختاری، کائولینیت شامل صفحات هشت وجهی آلومین و صفحات چهار وجهی سیلیس می باشد که به طور یک در میان قرار گرفته اند و تقریباً شامل ترکیبی از۵۴/۴۶ %، SiO2 و۵۰/۳۹ %، Al2O3 و ۹۶/۱۳%،H2O می باشد. نحوه قرارگیری اتمها در گروه کائولینیت در شکل۲ نشان داده شده است.
خواص فیزیکی و شیمیایی کائولین
خواص فیزیکی و شیمیایی کائولین، کاربرد آن را به عنوان یک کانی صنعتی تعیین می کند و این کاربردها توسط چندین عامل مانند شرایط زمین شناسی که ترکیب کلی نهشته های کائولین و خواص فیزیکی و شیمیایی کائولین در آن شرایط شکل گرفته است، کنترل می گردند.
اندازه ذرات
اندازه ذرات کائولین بین۵/۱-۲/۰میکرون متغیر و با سطح ویﮊه m²/kg 29000-10000می باشد. حد کنترلی تجاری، حد ۲ میکرومتر است. از کائولین درشت تر بعنوان پرکننده و از ذرات ریزتر معمولاً برای اندود استفاده می شود. شکل و محدوده اندازه ذرات کائولین از عوامل مهم کنترل کننده بسیاری از خواص آن از جمله درخشندگی، ویسکوزیته، مقاومت و انقباض است. اندازه ذرات با قطر گوی های کروی معادل (e.s.d) بیان می گردند و به وسیله نحوه رسوب گذاری از حالت معلق لخته ای رس در آب، تعیین می شوند.
اصلی ترین اجزای شیمیایی کائولین، سیلیس SiO2 و آلومین Al2O3 است که بیش از ۷۰% جرم کائولین را تشکیل می دهند. سیلیس و آلومین اجزاء اصلی (سخت) رس هستند که امکان گسترش ماتریس کریستالی به هم بافته شده ای را پس از احتراق در فرآیندهای تولید ظروف سفالی و چینی فراهم می آورند. وجود اکسید های آهن و تیتانیم برای سفیدی و روشنی کائولین، مضرند. وجود سیلیس اضافی به شکل کوارتز و کریستوبالیت عموماً مشکلات سایشی را در صنایع کاغذ ایجاد می کنند و وجود میکا و فلدسپات نیز می تواند روی روشنی و ویژگیهای سایشی آن تاثیر بگذارد.
تکلیس
کائولین بدون انجام فرآیندهای دیگر، در حدی که بتواند نقش پوزولان ایفا نماید، فعال نیست. کائولینیت در دمای معمولی، به شکل کریستالی (بلوری) پایدار وجود دارد و با هیدوکسید کلسیم به منظور تولید مواد سیمانی، واکنش نمی دهد.به منظور تبدیل کائولین به یک پوزولان فعال، باید تحت عملیات حرارتی قرار گیرد که این فرآیند تکلیس نام دارد.
کلسینه کردن کائولین، بر واکنش پذیری پوزلانی محصول بدست آمده تاثیر گذار است. حرارت، ابتدا آب جذب شده را از بین می برد. با افزایش درجه حرارت، آب بین لایه ای و آب ترکیبی از بین می رود. تاثیر درجه حرارت، محرک استفاده از آنالیز حرارتی متغیر (DTA) گردید. شکل ۵ منحنی DTAرس معمولی را نشان می دهد. نقطه اوج مهم گرماگیری (واکنش جذب گرما)، با حذف هیدروژن یا بیرون راندگی آب ترکیبی رخ می دهد. طبق شکل، مشاهده می شود که حداکثر گرماگیری معمولاً پس از حرارتهای بالاتر حداکثر گرمازایی (واکنش انتشار گرما) با تبدیل دوباره ماتریس غیربلوری (آمورف) رسوبی به بلور برای شکل گیری سیلیکاتها و اکسیدهای دما بالا اتفاق می افتد. در دمایی از تکلیس که به از بین رفتن هیدروکسیل منجر می گردد، رس در بهترین شرایط واکنش پذیری خود قرار دارد و ساختار شبکه ای بلوری متلاشی شده و در هم ریخته ای به دست می دهد و به مرحله ای انتقالی با واکنش پذیری بالا تبدیل می گردد. واکنش پذیری پوزولانی کلسینه شده، به از بین رفتن آب ساختاری لایه کائولینیت بلوری مربوط می شود که به تولید محصولی آمورف یا نیمه آمورف با مساحت ظاهری زیاد و واکنش پذیری شیمیایی زیاد منجر می گردد.
این موضوع نشان می دهد که طی عمل تکلیس، کائولینیت، آب شبکه، OH خود را از دست می دهد و ساختار کائولینیت فرو می ریزد. کائولینیت فروپاشی شده تمایل به دوباره چیدن ساختار زنجیری خود دارند. این زنجیرها متاکائولینیت نام دارند. در متاکائولینیت، شبکه Si-O در حد زیادی سالم و دست نخورده بجا می ماند و شبکه Al-O دوباره خود را سامان می دهد.
دمای تکلیس مورد نیاز به ماهیت و نوع کانی رسی و انرژی حرارتی لازم برای آزادسازی یونهای هیدروکسیل بستگی دارد. همچنین خرد کردن، به منظور شکستن ذرات متراکم و افزایش سطح بیشتر برای واکنش، سودمند است.
دمای تکلیسی که حالت فعال را بوجود می آورد معمولاً بین۸۰۰-۶۰۰ درجه سانتیگراد است.Ambroise و همکاران در سال ۱۹۸۵ تاثیر دمای تکلیس کائولینیت (۸۰۰-۶۰۰ درجه سانتیگراد) را بر افزایش مقاومت بتن تعیین نمودند. برای رسیدن به حداکثر مقاومت نمونه های۳ ،۷و۲۸ روزه، دمای بهینه تکلیس۷۰۰ درجه سانتیگراد بود. در کوششی دیگر، آنها نشان دادند که دمای تکلیس کمتر از ۷۰۰ درجه سانتیگراد به دستیابی به متاکائولینیت با فعالیت کمتر و استفاده از کائولینیت رسوبی بیشتر منجر می گردد. در دمای بالاتر از ۸۵۰ درجه، تبلور رخ می دهد و واکنش پذیری کاهش می یابد.
متاکائولین
متاکائولین که معمولاً رس “کلسینه شده” نامیده می شود، یک پوزولان سیلیکات آلومینیوم فعال است که بر اثر حرارت کائولینیت در رژیم دمایی مشخصی بدست می آید و فاز شیمیایی بدست آمده بر اثر عملیات حرارتی روی کائولین می باشد. ترکیب شیمیایی کائولینیت Al2O3,2SiO2,2H2O است که در اثر عملیات حرارتی در محدوده Cº۵۰۰-۴۰۰، آب آن بیرون رانده می شود تا سیلیکات آلومینیوم آمورف که متاکائولین نام دارد، بدست آید. محدوده حرارتی به ویژگیهای کائولین (کائولینیت با مقداری ناخالصی) از قبیل درجه تبلور و اندازه ذرات بستگی دارد.
متاکائولین، سفید رنگ است و رفتار پوزولانی دارد و می تواند با هیدروکسید کلسیم واکنش دهد و محصول مرکب آبدار سیلیکات کلسیم و آلومینیات کلسیم بدست آید. خردکردن متاکائولین و تبدیل آن به ذرات ریزتر، بر واکنش پذیری آن موثر است. همچنین درجه خلوص کائولین بر رنگ و واکنش پذیری آن تاثیر دارد. برای مثال، طبق ASTM 618 مقادیر حداقل لازم SiO2, Al2O3 و Fe2O3 در پوزولان کلاس N (natural) ، ۷۰% می باشد. بنابراین اگر منابع ناخاص کائولین بکار برده شوند باید بتوانند حداقل های آئین نامه ASTM 618 را تامین نمایند. مقادیر کمتر مواد سیلیسی و آلومینیومی به واکنش پذیری کمتر منجر می گردد که این مقدار واکنش پذیری با درشت تر شدن ذرات، باز هم کمتر می شود. همچنین رنگ آن نیز سفید نخواهد بود و بسته به نوع و مقدار ناخالصی می تواند به محصولی نامطلوب منجر گردد. متاکائولینی که در شکل ۷ نشان داده شده است به طور نمونه دارای اندازه ذرات با قطر حدود ۵/۱میکرومتر می باشد که بین (۱۲/۰-۱/۰میکرومتر) دوده سیلیس و (۲۰-۱۵ میکرومتر) برای سیمان پرتلند متغیر است.
بعنوان ترکیبی جدید برای تولید بتن با کارآیی بالا ، با جایگزینی متاکائولین بجای بخشی از سیمان مخلوط، می توان بتنی با مقاومت فشاری بتن ۱۱۰ مگاپاسکال بالاتر، تولید کرد. آزمایشها نشان داد که با استفاده از متاکائولین به مقدار ۵% تا۱۰% جرمی، بتنی به دست می آید که با خواص و کارآیی بتن تولید شده با دوده سیلیسی از نظر افزایش مقاومت و نفوذ یون کلرید و انقباض خشک شدگی و مقاومت در برابر درجات و سیکل های یخ زدن- آب شدن، برابری می کند.
مقایسه متاکائولین با سایر پوزولانها در مقاومت بتن
نتایج آزمایش مقایسه ای بر روی سه نمونه در جدول زیر آمده است. در روز اول، بتن حاوی دوده سیلیسی و سرباره، نسبت به بتن متاکائولینی مقاومت بیشتری از خود نشان دادند. همان طور که در جدول نشان داده شده است مقاومت متوسط بتن حاوی دوده سیلیسی و سرباره به ترتیب ۱۵و۲/۱۴مگاپاسکال است در صورتیکه برای بتن متاکائولینی این مقدار ۳/۱۱ می باشد. اما در روزهای بعدی، شرایط تغییر کرده و مقاومت بتن متاکائولینی در روزهای۳،۷و۲۸ در مقایسه با بتن حاوی دوده سیلیسی و سرباره، بیشتر است.
به طور کلی نتایج نشان می دهد، تاثیر متاکائولین در بالا بردن مقاومت بتن با سایر پوزولانها قابل مقایسه است. در واقع، مقاومت فشاری بتن متاکائولینی در روزهای اول در مقایسه با سایر پوزولانها بیشتر است. دوده سیلیسی و متاکائولین در مقایسه با سرباره، دانه بندی ریزتری دارند و به این دلیل، مقاومت بتن آمیخته شده با آنها به سرعت افزایش می یابد. سطح ظاهری زیاد ذرات متاکائولین، باعث می شود تا سیلیس آمورف سریع تر از دوده سیلیسی فاسد شود و همین، دلیل واکنش پذیری بیشتر متاکائولین نسبت به دوده سیلیسی و سرباره است. Malhorta در سال ۱۹۹۵ دریافت که بیشترین سرعت افزایش مقاومت در سنین اولیه بتن مخصوصاً بین ۱ و ۳ روز می باشد و او این پدیده را به سرعت بالای جذب آب در بتن متاکائولینی نسبت داد. در بتن متاکائولینی، متاکائولین با واکنش سریع پوزولانی، در مقاومت کوتاه مدت بتن شرکت می کند.
به طور کلی، مقایسه مقاومت با۱۰% جایگزینی ربطی به شاخص بکار رفته برای قیاس بین متاکائولین، دوده سیلیسی و سرباره ندارد چون هر یک از انواع مواد جایگزین، نسبت بهینه جایگزینی مربوط به خود دارند. مثلاً اگر جایگزینی به ۲۰% افزایش یابد، بتن متاکائولینی بهترین عملکرد را ندارد. معمولاً درصد های پایین جایگزینی (مانند۱۰%) مواد قابل جایگزین در سیمان(CRM) ،خواص سیمان را بالا می برند اما این مقدار، درصد بهینه نمی باشد. در این تحقیق، از۱۰% جایگزینی استفاده شد و با این مقدار، مقاومت همه بتن های متاکائولینی، دوده سیلیسی و سرباره ای افزایش یافت. استفاده از۱۰% جایگزینی متاکائولین، بررسی دشوار مقایسه عملکرد مواد جایگزین در افزایش مقاومت بتن را میسر سازد.